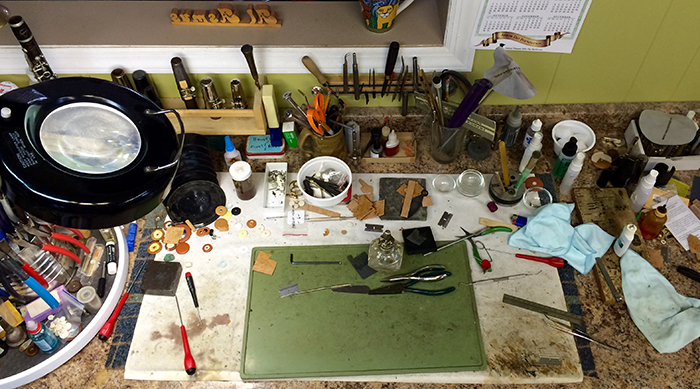
School’s out and it’s time to look at which instruments need repair. Some of the key things that need to happen with instruments over the summer are:
- Instrument cleaning (I recommend ultrasonic cleaning whenever possible)
- Cases vacuumed and cleaned
- Mouthpieces washed and inspected for damage
Today I’d like to offer some tips, from my perspective at the repair bench, to help you both correctly store instruments over the summer and be ready for the back-to-school season which sneaks up on us so fast.
Scheduling an Inspection
If you have a relationship with a local repair shop and can set-up an inspection time, do so before the end of June. Our shop does this with many of our local schools. Such an inspection offers two benefits. One is an extra set of eyes; the repair person may see or notice problems that could otherwise be overlooked. The second benefit is in providing a good working cost estimate. Making a spreadsheet with needed repairs and associated costs is a great tool for your administration and can result in getting a budget approved for school band instrument repairs.
Scheduling Repairs
Especially when specific parts have to be ordered, overhauling large instruments can take the entire summer. Again a good relationship with a local shop can be greatly beneficial. Rule one is to get your “biggest” jobs in as soon as possible.
If you require many of your instruments to fulfill marching obligation, don’t panic. Our shop, for example, early July is still sufficiently early in the summer to accommodate many school repairs. That being said, as mid-August approaches most shops stop answering their phones. While that might be a little bit of an exaggeration, it really can get busy from August 15th to Labor Day so plan ahead. The general public often thinks of the repair shop a week before band begins, often with the hope of bringing Aunt Sophie’s clarinet back to life.
Another thing to keep in mind when scheduling repairs is that sometimes it’s not necessary to send in the whole instrument. For example, if some neck cork needs to be replaced, it may be easier to simply send the neck. If a saxophone only requires some guard screws, it may not necessary to send anything at all.
Brass Instrument Storage
The most frequent repairs we see in our shop have to do with slides and valves that are stuck. This condition is usually combined with very dirty brass that needs a good cleaning after things are pulled apart. However, we have also received very clean instruments that have seized up. One cause could be that the instrument’s oils and grease has evaporated leaving slides and valves stuck in place.
If you have instruments likely to sit in storage for a long time, start by cleaning them. Then, instead of reassembling them, wrap the slides and valves in paper towels and place them in baggies. Ideally you’d store these baggies with the instrument, but if room doesn’t permit simply make sure you include a piece of paper with the instrument name and serial number in each bag (and mark the cases as well). Then when it comes time to use the instrument again, all you need to do is assemble, grease and oil as needed. No need for a trip to the repair shop.
Mold
Some instruments are especially susceptible to mold due to their design. For example, the bow of the saxophone is a common place for mold to develop. If you find mold growth in your instrument the best way to remove it is have it professionally cleaned by a shop that offers ultrasonic cleaning. They will disassemble the instrument, remove the keys, and fully clean it before reassembly.
Is there anything you can do to prevent future mold growth after such a cleaning? My shop has been testing a new technique. Today many shoes, electronics, and other items made overseas are shipped with silica gel bags in the packaging. The often say something like: “DO NOT EAT: THROW AWAY” on them. We see them in new instrument cases too; they’re there to absorb moisture and reduce mold growth. As a preventative measure, we’ve begun putting them in the cases of instruments that have been cleaned and treated for mold. So next time you come across a few of those bags save them (don’t throw them out) and toss them into your instrument case.
Pad Bugs
Another reusable item that can prevent problems during instrument storage is the thick plastic bag. When we receive new instruments from the factory, the cases are wrapped in heavy plastic before being placed inside a box. We keep these bags because they are made of very thick plastic (which is key). These bags come in handy for thwarting the efforts of the “pad bug” which is actually a moth or carpet beetle larvae.
Problems with pad bugs begin when the insect lays eggs on the seam of the case and the larvae crawl inside to feast on the wool found in felt clarinet and flute pads. If you have holes in your pads you know they’ve been there, although by then you’ve probably seen bug carcasses in the case as well.
If you’re going to store a woodwind instrument for an undetermined length of time, and you’d like to prevent pad bugs, bag it. Remember use a thick (3 to 4 mil) plastic bag and cover the entire instrument case. Cinch it up close and tie it tight with a zip or twist tie. This will make it difficult for the pad bug to stick to the case and make the initial entrance. This is especially important if it’s possible that the instrument will remain in storage for a period of years rather than months.
Hopefully you’ve found some useful ideas here. If you have any questions, remember your local repair shop is always ready and willing to help (but there might be a waiting line if you wait until August).